Resilient Rapid Reconfigurable Production Process Chains
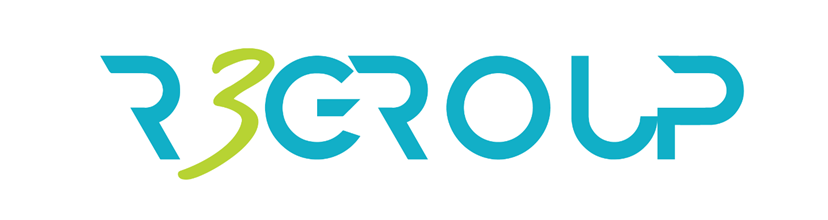
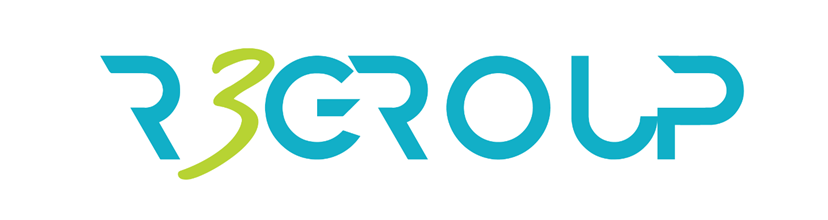
Acronym
R3GROUP
Started
1st January 2023
Ends
31st December 2026
Budget
€173 250
Strategic Objective
Foster sovereignity and competitiveness
Sector
Resilience supply chains
Activity Leader
Xanthi Bampoula
Business Development and Innovation Manager
EIT Manufacturing South East
About the project
R3GROUP will deploy reconfiguration strategies integrating technological, social and economic innovations to build a digital reference architecture and tools for resilient production. The project will comply with standardised Industry 4.0 interfaces and protocols.
Challenges
The manufacturing environment is changing. This is characterised by aggressive competition on a global scale and rapid changes in process technology. In response, businesses need to develop production systems that are easily upgradable and into which new technologies and new functions can be readily integrated.
Solutions
R3GROUP will leverage the six reconfigurability principles to advance technologies across five key pillars, fostering resilience through reconfigurability. This involves developing an Azure Analysis Services (AAS)-enabled platform for seamless horizontal and vertical integrability, alongside pioneering production tools aligned with the reconfigurable machine tool concept.
A digital toolkit will be deployed to swiftly assess reconfiguration impacts using multi-level digital twins. Additionally, innovative tools will be integrated to detect reconfiguration triggers, providing real-time awareness of the entire value chain’s status, including supply chain and market conditions. Comprehensive multi-level monitoring, control and quality assessment mechanisms will be employed to minimise the impacts of reconfiguration.
Expected results
The project is expected to benefit manufacturing processes because it will implement advanced reconfigurability and digitalisation technologies.
Expected results include:
- up to a 30% reduction in capital expenditure (CAPEX) for new markets,
- a 20-35% decrease in reconfiguration times
- improvements in overall equipment efficiency (OEE).
Additionally, scrap rates, lead times and material consumption will decrease, while quality control and production flexibility will improve.
By integrating digital twins, modular tooling, laser-based manufacturing and advanced data analytics, the project will enhance decision-making, optimise production and promote sustainable practices across various industries.